Enhancing Quality Control With Advanced Filtration Methods
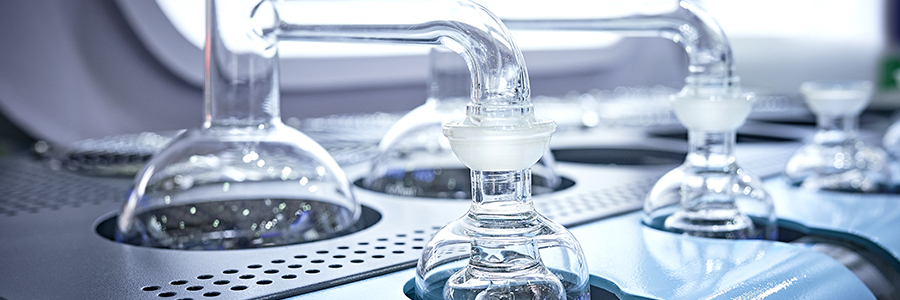
Quality control plays a vital role in every industry, as it ensures consistent delivery of products that surpass predetermined quality standards. Industries dealing with liquid-based products, like pharmaceuticals and water purification, rely on various filtration methods to maintain quality control. Employing advanced filtration techniques can significantly enhance quality control in these industries.
This article aims to elucidate the utilization of advanced filtration methods to improve quality control. By comprehensively understanding these advanced techniques in comparison to their conventional counterparts, we can grasp their profound impact on enhancing quality control. The article will delve into different advanced filtration methods, elucidating their applications and analyzing the outcomes they yield.
The importance of quality control in manufacturing
Quality control is a critical phase in the manufacturing process, as it directly influences the reputation of the manufacturer and the quality of the final product reaching the market. To ensure the desired quality of the end product, quality control must be implemented at every stage of the manufacturing process. This comprehensive process involves both inspection and measurement to guarantee that the product meets the required quality standards. Quality control thus is very important in any manufacturing process. Some of the points highlighting the importance are as follows:
- Consistency
In today’s interconnected market, maintaining consistent product quality is essential for building trust and meeting customer expectations. By implementing effective quality control measures at every stage of the manufacturing process, companies can ensure that their products consistently deliver the desired level of quality. This consistency fosters customer loyalty, supports smooth integration of products into downstream processes and strengthens the overall reputation of the manufacturing process.
- Cost Efficiency
While quality control may involve upfront costs, it ultimately leads to long-term cost efficiency. By preventing defects and ensuring the use of high-quality raw materials, quality control minimizes downtime, rework and waste. This results in optimized production processes, reduced resource consumption and lower overall costs. Investing in quality control measures upfront saves expenses associated with product failures, customer returns and potential damage to brand reputation.
- Waste Reduction
Implementing robust quality control measures significantly reduces waste in the manufacturing process. By using proper quality materials, conducting thorough inspections and optimizing process efficiency, manufacturers can minimize scrap, rework and rejected products. Waste reduction not only lowers production costs but also has positive environmental implications, promoting sustainability and resource conservation.
- Compliance
Compliance with industry regulations and standards is vital for manufacturers. Quality control ensures that products meet these requirements, preventing legal issues, penalties and reputational damage. By aligning their processes with guidelines and standards, manufacturers can demonstrate their commitment to safety, reliability and ethical practices.
- Risk Minimization
Quality control is instrumental in minimizing product defects and associated risks. By implementing rigorous inspection, testing and monitoring procedures, manufacturers can identify and address potential issues early on. This proactive approach reduces the likelihood of product failures, recalls and customer complaints. Additionally, comprehensive quality control measures enable manufacturers to trace and rectify the source of defects swiftly, improving overall product reliability and customer satisfaction.
Traditional filtration methods and their limitations
Filtration is essential in the manufacturing process, with more and more industries applying these filtration techniques for maintaining the desired quality. But while traditional filtration methods have been widely used and are generally effective, their limitations in terms of speed, equipment requirements and applicability to specific fluids hinder their large-scale applicability. Some of them are as follows:
Gravity Filtration
Gravity filtration utilizes the force of gravity to separate suspended solids from a solution. Over time, the heavier solids settle at the bottom of the tank while the filtered liquid is extracted from the top. This method is effective for solids with substantial mass. However, it comes with certain limitations:
- It is a relatively slow process and may require a significant amount of time to achieve the desired level of filtration.
- The filtration rate is dependent on gravity, which means that the filtration speed may vary based on the height and volume of the liquid being filtered.
- Gravity filtration is not suitable for filtering large volumes of liquids or fluids with high solid particle concentrations.
Cold Filtration
Cold filtration is commonly used in the pharmaceutical industry, as well as industries dealing with fatty acids, proteins or esters. By lowering the temperature of the fluid suspension, sedimentation of these substances is facilitated, allowing the separation of the chilled materials from the liquid above. However, cold filtration has its own set of limitations:
- Cold filtration can be a slow process, as it relies on reducing the temperature of the mixture, which may take a considerable amount of time, depending on the starting temperature and the desired level of cooling.
- Cold filtration is not suitable for all types of solids and liquids. Some substances may not solidify or separate efficiently at low temperatures, rendering cold filtration ineffective for those particular applications.
Sand Filtration
Sand filtration involves passing a fluid suspension through a bed of sand, where larger suspended solids are trapped in the voids of the sand particles. This method is effective for removing larger particles but may not be suitable for filtering out smaller suspended solids from the liquid suspension. While sand filtration has been widely used, it also has certain limitations:
- Sand filters are effective in removing larger particles and debris but may not be as efficient in capturing smaller particles or dissolved contaminants. Finer filtration techniques may be required for more thorough purification.
- Over time, the sand filter bed becomes saturated with captured particles, leading to a decrease in filtration efficiency. Regular backwashing, which involves reversing the flow of water through the filter to dislodge trapped particles, is necessary to maintain optimal performance.
Mechanical Filtration
Mechanical filtration is a widely used technique that employs filters to separate solids from liquids. Surface filtration captures solids on the outer surface of the filter, while depth filtration traps solids throughout the filter’s depth. However, mechanical filtration also has its limitations:
- The effectiveness of mechanical filtration is highly dependent on selecting the appropriate pore size of the filter medium. If the pore size is too large, smaller particles may not be effectively removed. Conversely, if the pore size is too small, the filtration process may become slow and prone to clogging.
- Mechanical filters have a finite life span, as they become progressively clogged with trapped particles. Regular maintenance and replacement of filter media are necessary to maintain optimal filtration performance.
Advanced filtration methods
Advanced filtration methods such as ultrafiltration, nanofiltration and reverse osmosis offer improved quality control compared to traditional methods. They enable selective separation and concentration of molecules based on size, charge and solubility, effectively removing impurities, contaminants and unwanted components from the sample. These advanced methods provide researchers with enhanced control over the composition and purity of their samples, contributing to more accurate and reliable experimental results.
Ultrafiltration
Ultrafiltration is a powerful technique employed in various scientific and industrial applications to separate macromolecules based on their size. It utilizes a semipermeable membrane with a specific pore size that acts as a molecular sieve. This membrane allows smaller molecules, solvents and ions to pass through while retaining larger molecules, such as proteins, DNA and nanoparticles. The process of ultrafiltration involves several key steps to achieve efficient separation and purification.
Sample Loading: The first step in ultrafiltration is the loading of the sample onto the ultrafiltration device. The sample typically contains a mixture of macromolecules, including the target molecule and other impurities or contaminants.
Application of Pressure: After loading the sample, pressure is applied to drive the solvent and smaller molecules through the semipermeable membrane. The pressure can be applied through different methods, such as centrifugation or using a pressure-driven system.
Filtration: As the pressure is applied, the solvent and smaller molecules pass through the membrane, while the larger macromolecules are retained on the membrane surface. The membrane acts as a molecular sieve, allowing molecules below a certain size to pass through its pores.
Collection of the Filtrate: The filtrate, which contains the smaller molecules and solvent, is collected. This filtrate may be further processed or analyzed as needed for downstream applications.
Concentration of Target Molecule: In some cases, it is desirable to concentrate the target macromolecule for further analysis or experimentation. This can be achieved by repeatedly circulating the filtrate through the membrane or by applying a concentration gradient across the membrane. Concentration steps are particularly useful when working with dilute samples or when higher sensitivity is required in subsequent assays.
Removal of Contaminants: Ultrafiltration also aids in removing contaminants or unwanted substances present in the sample. By selecting a membrane with an appropriate molecular weight cutoff (MWCO), molecules below the cutoff can be efficiently eliminated from the sample. This helps improve the purity and quality of the target macromolecule.
Buffer Exchange: Ultrafiltration allows for buffer exchange, enabling researchers to transition the sample from one experimental condition to another. By passing the sample through the ultrafiltration membrane and replacing the original buffer with a desired buffer solution, researchers can adjust the sample environment, optimize conditions or remove unwanted substances that may interfere with downstream assays.
Ultrafiltration, as an advanced filtration method, offers several advantages over traditional methods. Unlike traditional methods that rely on gravity or simple sieving mechanisms, ultrafiltration utilizes a semipermeable membrane with a defined pore size. This allows for more precise separation and concentration of macromolecules based on size, resulting in improved purification and removal of contaminants. Additionally, ultrafiltration enables buffer exchange and facilitates the removal of smaller impurities that may be difficult to eliminate using traditional methods.
Nanofiltration
Nanofiltration is a membrane-based filtration technique that offers precise separation of molecules based on their size and charge. It employs a specialized nanoporous membrane with smaller pore sizes compared to ultrafiltration. Nanofiltration is particularly effective in selectively removing specific ions, organic matter and contaminants from the solution. The smaller pore sizes of the membrane allow for precise separation, resulting in enhanced purification compared to traditional filtration methods. This membrane allows the selective passage of ions and molecules based on their charge and size. The process of nanofiltration involves several key steps.
Sample Loading: The first step in nanofiltration is the loading of the sample onto the nanofiltration device. The sample may contain a mixture of ions, molecules and contaminants.
Application of Pressure: Once the sample is loaded, pressure is applied to drive the solvent and solutes through the nanoporous membrane. The pressure can be generated using a pressure-driven system or other methods, depending on the setup.
Separation of Solutes Based on Charge and Size: The nanoporous membrane used in nanofiltration has smaller pore sizes compared to ultrafiltration membranes. This enables the selective separation of solutes based on their charge and size. The membrane selectively retains larger ions and molecules while allowing smaller ions and molecules to pass through.
Collection of the Permeate: The permeate, which contains the smaller ions and molecules that passed through the membrane, is collected. This permeate is typically the purified fraction of the sample that has undergone separation based on charge and size.
Compared to traditional methods, nanofiltration offers several advantages. It provides more precise separation, based on both size and charge, enabling the selective removal of specific ions and contaminants. The smaller pore sizes of the membrane allow for greater control and efficiency in quality control processes. Additionally, nanofiltration is a valuable tool for applications where a higher level of purification and separation is required, such as in water treatment, food and beverage processing, and pharmaceutical manufacturing.
Reverse Osmosis
Reverse osmosis is a filtration technique that utilizes a semipermeable membrane to separate solvents from solutes by applying pressure. The membrane allows the solvent to pass through while retaining the solutes, effectively purifying the solution. Reverse osmosis improves quality control by effectively removing dissolved impurities, salts and contaminants from the solution. The resulting permeate is a purified solvent that can be used in various applications where high-quality and low-impurity solvents are required. The process of reverse osmosis involves several key steps.
Sample Loading: The first step in reverse osmosis is to load the sample into the reverse osmosis system. The sample may contain dissolved impurities, salts and contaminants.
Application of Pressure: Pressure is then applied to the solution. This pressure is higher than the osmotic pressure, which is the force that prevents the solvent from passing through the semipermeable membrane. The applied pressure allows the solvent molecules to overcome the osmotic pressure and pass through the membrane.
Separation of Solvent and Solute: The semipermeable membrane used in reverse osmosis allows the solvent, typically water, to pass through while retaining the solutes. The membrane has very small pores that prevent the passage of solutes, including impurities, salts and contaminants.
Collection of the Permeate: The permeate, which is the purified solvent, is collected on the other side of the membrane. It is free from the majority of dissolved impurities, salts and contaminants present in the original sample.
Compared to traditional filtration methods, reverse osmosis offers superior purification capabilities. It can effectively remove a wide range of impurities and contaminants that may not be efficiently eliminated by other filtration techniques. Reverse osmosis is widely used in industries such as water treatment, water purification, desalination, food and beverage processing, and pharmaceutical manufacturing to achieve high-quality and purified solvents or water.
Applications of advanced filtration in manufacturing
Advanced filtration techniques find wide application across various industries due to their ability to filter different types of substances. Numerous manufacturing processes in different sectors rely on these advanced filtration methods. Several industries that incorporate advanced filtration techniques in their manufacturing processes include:
Pharmaceutical Industry
The pharmaceutical industry heavily relies on various advanced filtration techniques, particularly in the downstream process of manufacturing. Advanced filtration methods, such as membrane filtration, play a crucial role in eliminating bacterial cells, viruses and cellular debris from pharmaceutical products. Additionally, techniques like reverse osmosis are utilized to obtain purified water, which is essential for different stages of the manufacturing process. These advanced filtration methods, including various membrane filtration techniques, significantly enhance the overall product quality in the pharmaceutical industry.
Automotive Industry
The automotive industry implements multiple processes that necessitate contamination-free substances during manufacturing. Within environments like paint booths, it is vital to ensure the absence of dust, smoke or other contaminants to achieve a smooth and even paint coat. To achieve this, advanced filtration techniques like electrostatic filters are employed to effectively remove dust and other impurities from the air. Clean air is also crucial in manufacturing processes such as engine assembly and electronics production, where advanced filtration methods provide the required air quality standards.
Electronics Industry
Industries involved in the manufacturing of sensitive electronics, including computer chips and PCBs, require a highly filtered and very clean air supply. For instance, during the CPU circuit etching process in chemical vapor deposition chambers, a clean and sterile air supply is essential to prevent any defects in the final product. Advanced filtration techniques, such as electrostatic air filters, are employed to ensure the necessary air cleanliness. These filters are also utilized to remove contaminants from the air exhausted by the industry, thereby reducing environmental pollution.
Water Treatment Industry
Advanced filtration techniques play a critical role in the water treatment industry. While traditional filtration methods are employed initially to clean dirty water, advanced filtration techniques are essential for rendering water safe for consumption or environmental use. Membrane filtration methods, like ultrafiltration and microfiltration, effectively remove biological contaminants present in the water. Techniques such as nanofiltration and reverse osmosis are employed to remove trace ionic contaminants and desalinate water, respectively, ensuring the production of clean drinking water.
Analyzing results of advanced filtration techniques
The effectiveness of filtration techniques in any industry can be analyzed by considering certain parameters. Based on the analysis of these parameters, the manufacturer determines whether the particular filtration process is efficient for the manufacturing process or not. Some criteria that measure the success of the advanced filtration techniques are as follows:
Flow Rate
Flow rate plays a crucial role in determining the effectiveness of filtration techniques in different manufacturing processes. The ability of a filtration system to maintain a consistent flow rate over time is a desirable characteristic. Depending on the requirements of the specific industry — whether a faster or slower flow rate is needed — the filtration technique or system can be evaluated based on its ability to maintain the desired flow rate while ensuring efficient filtration. Flow rate serves as an important measure to assess the success of a filtration technique in various applications.
Filtration Efficiency
Filtration efficiency is a key parameter for evaluating the results of advanced filtration techniques. It indicates the capability of the filtration system to effectively remove contaminants to the desired level. Advanced filtration methods are designed to achieve high filtration efficiency, ensuring the removal of even the smallest contaminants from the fluid. The ability to consistently filter out contaminants according to the desired standards is crucial in determining the success of a filtration technique.
Fouling
Fouling, which involves the accumulation of filtered substances on filtration membranes or within the filtration system, is an important factor to consider when assessing filtration techniques. The rate of fouling directly affects the life span of the filter and the frequency of maintenance required. Higher fouling rates result in more frequent downtime for maintenance, leading to reduced manufacturing efficiency. Evaluating the level of fouling helps determine the overall effectiveness and operational costs associated with a filtration technique.
Cost Effectiveness
Cost effectiveness is a vital aspect to consider when selecting advanced filtration techniques. While these techniques often involve significant initial investments, it is important to assess their cost in relation to their purpose in the manufacturing process. Industries handling sensitive equipment and products may benefit from higher-cost, high-performance advanced filtration techniques to ensure product quality and the longevity of machinery. Choosing the right filtration technique involves careful evaluation of the cost-to-benefit ratio, considering both the quality of the end product and the efficient operation of sensitive manufacturing equipment.
Process filtration solutions in biopharma
Filtration techniques are integral to manufacturing processes and have a direct impact on the quality of the end products. Advanced filtration techniques have become essential in industries aiming for improved filtering efficiency and better product quality. While traditional and older methods of filters are still used, they often fall short in meeting the effectiveness required for producing high-quality products.
Advanced techniques such as electrostatic filters and membrane filtration have emerged to support sensitive manufacturing processes and ensure consistent quality. Various industries, including pharmaceuticals, automotive and electronics, rely on advanced filtration methods tailored to their specific needs. Evaluating the success of filtration techniques in different manufacturing processes involves analyzing parameters such as filtration efficiency, flow rates, fouling and cost-effectiveness. This enables informed decisions regarding the most suitable filtration technique for a particular manufacturing process.
For a detailed understanding of advanced filtration techniques and their significance in quality control visit Avantor.